El chasis es la estructura interna que sujeta, da forma y aporta rigidez a un vehículo, es decir, la base esencial de todo vehículo, sujeta todos los componentes mecánicos tales como, suspensión, ruedas y el motor propulsor.
-Existen diferentes tipos de estructuras, a continuación pasaremos a definir las mas importantes;
Chasis en H o en escalera:
Consiste en dos largueros laterales de chapa laminada con perfil cajeado , paralelos o no, unidos mediante una serie de travesaños. Este tipo se ha convertido en el estándar para la mayoría de los tipos de automóviles.
Su diseño es muy básico, pero mayor desventaja es que hay poca profundidad a la estructura general dándole un centro de gravedad muy bajo. Lo podemos encontrar en la mayoría de los autos clásicos y en camiones, debido a su gran solidez.

Chasis-plataforma:
Una solución intermedia entre la carrocería autoportante y la instalada sobre un chasis es un proyecto consistente en lo que se llamó carrocería con plataforma de chasis. En este diseño se construye como un chasis de plancha al que se le sujeta el resto de la carrocería.
Este proyecto tuvo un aceptable éxito al ser aplicado a algunos modelos de turismos construidos para dar un servicio intermedio y poder ser utilizados en carretera y también en malos caminos de bosque o campo.
Nos referimos, desde luego, a una época muy anterior a la de los llamados todoterreno 4x4 que vinieron a solucionar esta ambivalencia con la máxima eficacia.
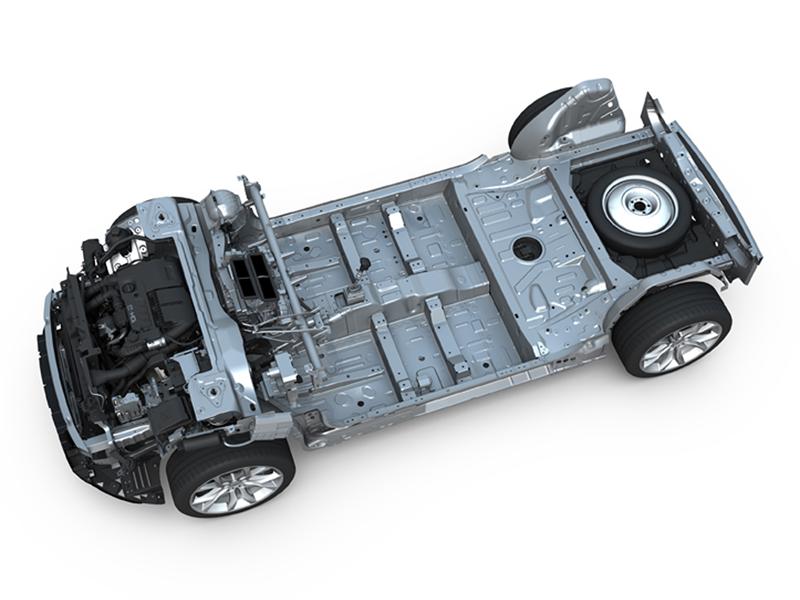
Chasis supperleggera o tubular:
La carrocería tubular o superleggera , es un tipo de carrocería utilizado en vehículos clásicos deportivos de mediados del siglo XX y por los grupos B de los años 80. Fue creada por el carrocero italiano Touring en 1937 y se utiliza como estructura del vehículo una red de finos tubos metálicos soldados, recubierta después con láminas metálicas, frecuentemente de metales exóticos tales como aluminio o magnesio.
Esta técnica consigue una carrocería de gran rigidez y resistencia con muy poco peso. Por otra parte, la fabricación es muy cara y laboriosa. La técnica todavía se utiliza en modelos deportivos hechos a mano.
Este diseño se emplea sobre todo en vehículos de competición, en los que la carrocería exterior tiene una misión estética y aerodinámica.
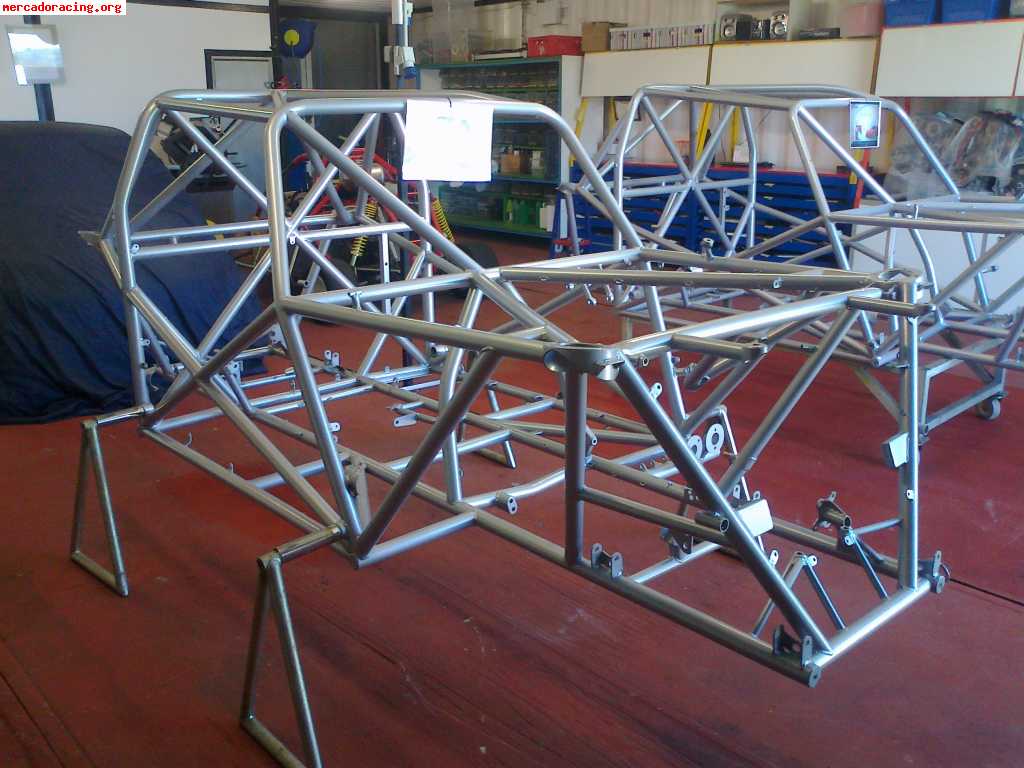
Chasis wishbone o columnar:
Tiene el propósito de conectar el eje delantero con el trasero, se utiliza sobre todo en los roadsters.
Presentan grandes desventajas entre ellas la mas importante es que son muy pesados para poder ser usados en autos deportivos y demasiado caros para ser producidos en masa.

Chasis autoportante:
Es la carrocería más empleada en automóviles, es una técnica de construcción de chasis en la cual la chapa externa del vehículo soporta parte o toda la carga estructural del vehículo, se compone de un conjunto de bastidor y carrocería unidos entre sí remachados o soldados que forman la carrocería completa.
Se parte del concepto de hacer una estructura metálica envolvente constituida por la unión de elementos de chapa de diferentes formas y espesores, es decir, se construye una caja resistente que se soporta a si misma y a los elementos mecánicos que se fijen sobre ella. El primer automóvil que utilizó este sistema, fue el Lancia Lambda, después se unieron el Chrysler Airflow y el Citroën Traction Avant.

-Existen diferentes distribuciones mecánicas, entre ellas podemos destacar las siguientes;
La distribución mecánica de los vehículos es el lugar donde va situado el motor del vehículo, podemos encontrar tres grandes grupos:delantera, trasera y central.
La distribución mecánica delantera es la posición más habitual, ya que debido a esta localización se permite un mayor espacio del habitáculo para pasajeros e incluso ampliando el espacio del maletero.
Además de mejorar la amplitud y la comodidad, dicha situación permite mejorar la refigeración del motor por el acto del aire incidiendo en el frontal del vehículo.
Aunque encontremos el motor, transmisión en la parte frontal del vehículo, podemos encontrar tracción delantera, trasera o total.
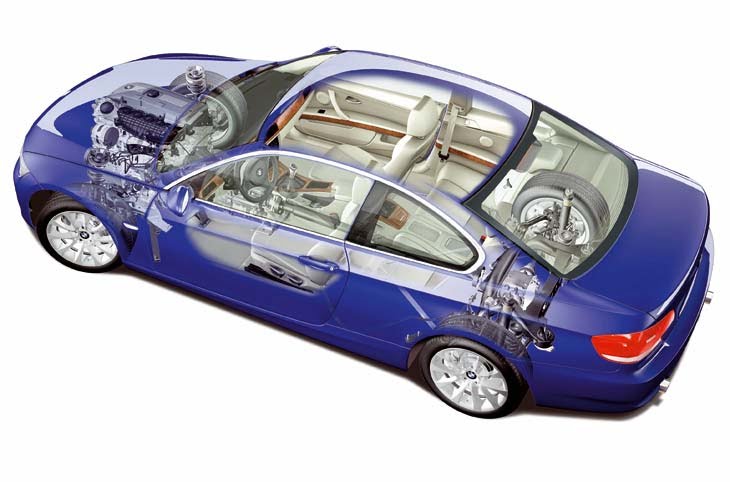
La distribución mecánica con motor trasero también llamado, tracción trasera es el sistema en el que la transmisión del movimiento del motor de un vehículo se realiza sobre el eje trasero y va situado en la parte trasera del vehículo.
Este motor tiene como ventajas, mejor adherencia de las ruedas en la fase de aceleración debido a la transferencia de peso, mejor reparto de pesos que permite situar el centro de gravedad lo más cerca posible del centro de las 4 ruedas.
Como desventajas podemos citar las siguientes, un mayor coste constructivo, menos espacio disponible en habitáculo, mayor peso, mayor facilidad de perder adherencia en curva (especialmente con vehículos muy potentes) por la componente centrífuga de las fuerzas sobre el neumático.
Otra de las principales desventajas es la falta de refrigeración, ya que no ocurre lo mismo que los de disposición delantera y por lo tanto hay que abrir unas tomas de aire en la zona del motor para ayudar a su refrigeración, recordad, que son motores que funcionan en unos regímenes de vueltas elevados.

Se denomina motor central, cuando el mismo se encuentra entre el eje delantero y el eje trasero del vehículo.

-Distribución de volúmenes y clasificación de los vehículos en función de la misma.
Monovolumen: es una carrocería en la que no se diferencia más de un volumen. La zona del motor, la cabina y el maletero están completamente integrados. Generalmente, un monovolumen es más alto que un automóvil de turismo (1,60 a 1,80 metros contra 1,40 a 1,50 metros). Los monovolúmenes grandes y algunos compactos (desde 4,40 metros en adelante) tienen frecuentemente tres filas de asientos, mientras que los más pequeños solo tienen dos filas.

Dos volúmenes: articulan un volumen para el capó con el motor y un volumen que combina el compartimiento de pasajeros y de carga se caracterizan al tener portón para poder acceder al maletero.

Tres volúmenes: se distinguen claramente los tres volúmenes: un volumen para el capó con el motor, otro volumen para el habitáculo y un tercero para el compartimento de carga.
Los sedanes y numerosos cupés también los son. A la hora de acceder al maletero, se caracterizan porque solo se abre una puerta, es decir, no incluye la luna trasera como un portón.
![]() |
Audi A3 sedan: primer vehículo compacto de 3 volúmenes |
- Identificación de vehículos por VIN
El número de bastidor, número de identificación o número VIN (del inglés Vehicle Identification Number) permite la identificación inequívoca de todo vehículo a motor. Este número va impreso o remachado en una placa y puede ir situada en diferentes partes del automóvil (borde inferior del parabrisas del coche, en el vano del motor, en la puerta del conductor, etc.), va a permitir proteger los vehículos de robos, manipulación o falsificación.
Hasta 1980 no había una norma clara que identificase los vehículos de una forma homogénea por parte de todos los fabricantes, sino que cada cual tenía su regla para poder identificar cada vehículo que salía de sus factorías. No fue hasta 1980, cuando la aparición del estándar ISO 3779 sirvió para definir un VIN o código de bastidor de 17 cifras y letras, que no incluyen las letras I, O y Q, y que permitió a todos los fabricantes seguir un mismo criterio a la hora de identificar sus vehículos.
El número VIN, que contiene el WMI, VDS y VIS, está compuesto de distintas partes o secciones. Dependiendo del origen del vehículo su nomenclatura es distinta. El estándar ISO 3779 es el empleado en la Unión Europea, mientras que en Estados Unidos y Canadá se emplea otro sistema distinto.
En la siguiente tabla se representan en resumen las distintas secciones que conforman al número VIN:

Para Europa, los 17 caracteres que componen el VIN ofrecen la siguiente información:
- la primera cifra indica el país de fabricación. Así, por ejemplo si se tiene la numeración del 1 al 4 indica que el vehículo fue fabricado en Estados Unidos, el 2 en Canadá, el 3 en México, o bien pueden aparecer también letras si la procedencia es de otros países, como J para Japón, K para Corea, S para Inglaterra, W para Alemania, Y para Suecia, Z para Italia, entre otros (para más información, ver Apartado 3 de este Tutorial "WMI o Identificador Mundial del Fabricante");
- la segunda cifra indica la marca según la siguiente codificación: Audi (A), BMW (B), Buick (4), Cadillac (6), Chevrolet (1), Chrysler (C), Dodge (B), Ford (F), GM Canada (7), General Motors (G), Honda (H), Jaguar (A), Lincon (L), Mercedes Benz (D), Mercury (M), Nissan (N), Oldsmobile (3), Pontiac (2 o 5), Plymounth (P), Saab (S), Saturn (8), Toyota (T), Volvo (V) (para más información, ver Apartado 3 de este Tutorial "WMI o Identificador Mundial del Fabricante");
- la tercera cifra indica el fabricante del vehículo (para más información, ver Apartado 3 de este Tutorial "WMI o Identificador Mundial del Fabricante");
- las cuatro siguientes identifican el modelo y se asignan en la homologación, según sean las características del vehículo, tipo de chasis, modelo de motor, entre otros;
- el octavo carácter indica los sistemas de retención que dispone el vehículo: pretensores en los cinturones, número de airbag, etc.;
- el noveno es un dígito de control o de verificación, que se obtiene con la asignación de valores a las letras del abecedario omitiendo la I, O, Q y Ñ según la norma 3779 de la Organización Internacional para la Estandarización como se muestra la siguiente tabla:
Este número es multiplicado por el valor asignado de acuerdo al peso de vehículo y a través de una ecuación preestablecida se obtiene el número que va en esta posición (ver un ejemplo de cómo calcular este dígito de control en el Apartado 4 de este Tutorial);
- el décimo, informa del año de fabricación. Desde 1980 a 2000, se indicaba por una letra: 2000 (Y), 1999 (X), 1998 (W), 1997 (V). De 2001 a 2009 por un número: 2001 (1), 2002 (2), 2003 (3). En 2010 la lista se reiniciará cíclicamente;
- el undécimo identifica la planta en la que fue ensamblado el vehículo;
- el resto identifica el vehículo individual. Puede tratarse de un simple número o un código del fabricante que indique particularidades como las opciones instaladas, el tipo de motor, transmisión u otras, o ser simplemente la secuencia en la línea de producción del vehículo de acuerdo al fabricante.
¿Qué es la contraseña de homologación?
La Contraseña de Homologación aparece en la Tarjeta ITV de los vehículos que es expedida por una estación ITV española. También aparece en el Certificado de Conformidad si el vehículo es importado, y cuyo documento es muy recomendable disponer de él si se pretende legalizar el vehículo importado en España.
La estructura de una contraseña de homologación es la siguiente:
e6*93/81*0023*00
donde:
e: significa Unión Europea;
6: identifica el país de homologación, según la lista adjunta:
1 Alemania, 2 Francia, 3 Italia, 4 Países Bajos, 5 Suecia, 6 Bélgica, 9 España, 11 Reino Unido, 12 Austria, 13 Luxemburgo, 17 Finlandia, 18 Dinamarca, 21 Portugal, 23 Grecia, 24 Irlanda
93/81: es la directiva de aplicación (también puede ser 92/53);
0023: es el número de homologación;
00: número de modificación o de la revisión desde la homologación inicial

Bueno chavales y eso es todo por hoy, como siempre cualquier duda me dejáis un comentario, hasta la próxima entrada un saludo y a cuidarse!