Obtención del Hierro y su uso industrial
Una de las
actividades más importantes en el desarrollo de la civilización es la obtención
de metales con los que fabricar herramientas. Este conjunto de procesos es
bastante complejo, y específico para cada metal.
Pero siempre causa un
gran impacto sobre el medio ambiente, que debe minimizarse en lo posible.
Vamos a ver como
ejemplo la obtención del mineral de hierro, y su transformación en las
distintas formas de hierro y acero; a esto se le denomina siderurgia.
La industria de fabricación de aceros es de las más importantes de cualquier
sector industrial.
Primero hay que sacar
el mineral de la mina, que suele ser subterránea en el caso del mineral de
hierro, aunque el desbordante crecimiento de la construcción ha multiplicado el
aprovechamiento de las minas a cielo abierto; este tipo de mina genera un
enorme impacto, hasta el punto de que genera el 75% de todos los residuos
industriales de España, según el Instituto Nacional de Estadística.

El transporte del
mineral dentro y fuera de la mina obliga al uso de gran número de vehículos.
Cuando llega el
mineral de hierro a la industria, se procesa junto a caliza y carbón mineral en
los altos hornos, de forma semejante a grandes chimeneas, donde
ocurren las reacciones que transforman el óxido de hierro inicial en hierro
metálico.
Los altos hornos
consumen una enorme cantidad de energía, y producen muchos gases que terminan,
en mayor o menor medida, en la emisión de gases que se difunden en la atmósfera
circundante.
El hierro así
obtenido contiene una gran cantidad de impurezas, entre ellas el carbono, que
si excede cierta proporción, convierte a la aleación en frágil y muy dura.
Para eliminar las
impurezas y el carbono en exceso se usan los convertidores, que
mediante calentamiento e inyección de gases convierten la mezcla en acero,
que no es más que hierro con carbono, al que se puede añadir la proporción
deseada de otros elementos.
El
hierro es el metal duro más usado, con el 95 % en peso de la producción
mundial de metal. El hierro puro
(pureza a partir de 99,5 %) no tiene demasiadas aplicaciones, salvo
excepciones para utilizar su potencial magnético. El hierro tiene su gran
aplicación para formar los productos siderúrgicos,
utilizando éste como elemento matriz para alojar otros elementos aleantes tanto
metálicos como no metálicos, que confieren distintas propiedades al material.
Se considera que una aleación de hierro es acero si contiene
menos de un 2,1 % de carbono; si el porcentaje es mayor, recibe el nombre de fundición.
El acero es indispensable debido a su bajo
precio y tenacidad, especialmente en automóviles, barcos y componentes estructurales
de edificios.
Las aleaciones férreas presentan una gran
variedad de propiedades mecánicas dependiendo de su composición o el
tratamiento que se haya llevado a cabo.
Producción del acero
Se denomina acero a las aleaciones del hierro con el carbono
y otros elementos, que al calentarlas hasta altas temperaturas, pueden ser
sometidas a la deformación plástica por laminado, estirado, forjado, estampado.
El acero contiene hasta 2% de carbono y ciertas cantidades de silicio y
manganeso y también impurezas nocivas: fósforo y azufre, las cuales no se
pueden eliminar por completo del metal por los métodos metalúrgicos. Aparte de
estas impurezas los aceros pueden contener algunos elementos de aleación:
cromo, níquel, vanadio, titanio y otros.
El acero se elabora
primordialmente por la transformación del hierro fundido en forma de arrabio. La
tarea de la transformación del arrabio en acero se reduce a la extracción de
las cantidades sobrantes de carbono, silicio, manganeso y las impurezas nocivas
que contiene.
Esta tarea se puede llevar a cabo porque el carbono y las otras
impurezas, bajo la acción de altas temperaturas, se unen con el oxígeno de un modo mas enérgico que el
hierro y pueden extraerse con pérdidas insignificantes de hierro.
Para
la transformación del arrabio a acero se utilizan dos métodos generales:
1.- El método de los convertidores.
2.- El
uso de hornos especiales.
La
esencia del método de los convertidores para la obtención del acero consiste en
que a través del hierro fundido líquido cargado al convertidor, se inyecta
aire, que burbujea dentro de la masa fundida y cuyo oxígeno oxida el carbono
y otras impurezas.
El convertidor presenta un recipiente en forma de pera, soldado con
chapas gruesas de acero y revestido interiormente con material refractario. En
la parte central del convertidor, exteriormente se hallan dos tetones
cilíndricos llamados muñones que sirven de soporte y permiten girar el
convertidor. Uno de los muñones es hueco y se une con el tubo conductor de
aire. Del muñón el aire es conducido por un tubo y por la caja de aire al
fondo. En el fondo del convertidor están las toberas a través de las cuales el
aire se suministra al convertidor a presión. También se utiliza la ayuda de oxígeno con lo que el proceso se hace mas rápido y eficiente.

Para
cargar el convertidor este se hace girar de la posición vertical a la
horizontal, se agrega el arrabio fundido y se regresa el convertidor a su
posición vertical, en ese momento se pone en marcha el soplado. El volumen de
metal incorporado constituye de 1/5 a 1/3 del volumen de la altura de la parte casi
cilíndrica.
1.- Convertidor con revestimiento ácido: (procedimiento Bessemer) utilizado
para los arrabios con una cantidad mínima de fósforo (0.07%) y azufre (0.06%).
2.-
Convertidor con recubrimiento básico: (procedimiento Thomas) utilizado para los
arrabios con mayor abundancia de fósforo (hasta 2.5%).
El
uso razonable del hierro fundido y la mas completa utilización de la chatarra
ferrosa, se logra al producir aceros en horno.
A diferencia de los convertidores, los hornos de producción de acero son
cámaras revestidas con material refractario donde se vierte arrabio en lingotes
o líquido y chatarra ferrosa, junto con otros materiales que sirven de
fundentes y aportadores de elementos necesarios para los procesos de oxidación.
Luego el material se calienta por diversos métodos hasta su fundición con lo
que comienzan los procesos de oxidación de las impurezas y del propio hierro y
se va formando la escoria.
En estos hornos no se inyecta aire a la masa de metal fundido como en los
convertidores, por el contrario los procesos de oxidación de las impurezas se
realizan al interactuar los componentes de la escoria con el metal fundido de
abajo.
Para lograr acero líquido dentro del horno se necesita una fuente intensa de
calor que interactúe con el contenido del horno y pueda fundir el metal. Se
distinguen dos tipos generales:
1.- Los que usan combustible (hornos Martin).
2.- Los
que usan electricidad (de arco eléctrico y de inducción).
En
los hornos Martin (combustible) se elabora probablemente la mayor parte del
acero producido en el mundo. En estos hornos el combustible utilizado puede ser
gaseoso, líquido, sólido en polvo o sus combinaciones.

Clasificación de los aceros por %C
Los aceros se pueden clasficiar en
función de varios criterios, esto da lugar a varias clasificaciones, la más
utilizada de todas ellas es la clasificación en función del porcentaje
de carbono disuelto:
El porcentaje de carbono disuelto en
el acero condiciona las propiedades del mismo. Así cuanto mayor sea el
porcentaje de carbono disuelto en el acero, éste presenta más dureza y más
resistencia a la tracción. Teniendo esto presente es posible clasificar los
aceros en:
Contenido
límite para aceros no aleados
|
|
Elemento
|
Contenido
|
Aluminio
|
0,10
|
Bismuto
|
0,10
|
Boro
|
0,0008
|
Cobalto
|
0,10
|
Cobre
|
0,40
|
Cromo
|
0,30
|
Manganeso
|
1,60
|
Molibdeno
|
0,08
|
Novio
|
0,05
|
Níquel
|
0,30
|
Plomo
|
0,40
|
Silicio
|
0,60
|
Titanio
|
0,05
|
Vanadio
|
0,10
|
Volframio
|
0,10
|
Lantánidos
|
0,05
|
Otros excepto (P, C, N y O)
|
0,05
|
Por otro
lado es posible hablar de aceros aleados y aceros no aledos. Se consideran
aceros no aleados aquellos en los cuales el porcentaje de
elementos químicos que forman el acero no supera el valor indicado en la
siguiente tabla:
Contenido
límite para aceros no aleados
|
|
Elemento
|
Contenido
|
Aluminio
|
0,10
|
Bismuto
|
0,10
|
Boro
|
0,0008
|
Cobalto
|
0,10
|
Cobre
|
0,40
|
Cromo
|
0,30
|
Manganeso
|
1,60
|
Molibdeno
|
0,08
|
Novio
|
0,05
|
Níquel
|
0,30
|
Plomo
|
0,40
|
Silicio
|
0,60
|
Titanio
|
0,05
|
Vanadio
|
0,10
|
Volframio
|
0,10
|
Lantánidos
|
0,05
|
Otros excepto (P, C, N y O)
|
0,05
|
Aquellos
aceros que tienen mayor porcentaje de los indicados en las tablas son
requeridos para utilizaciones especiales, y están recogidos en las
normas UNE.
Constituyentes de los aceros
FERRITA (Feα )
Es una
solución sólida de carbono en hierro alfa.
Su
solubilidad a la temperatura ambiente es del orden de 0.008% de carbono, por lo
que se considera hierro puro. La máxima solubilidad de carbono en el hierro
alfa es de 0.02% a 723°C.
La ferrita
es la fase más blanda y dúctil de los aceros, cristaliza en la
red BCC, tiene una dureza de 90 Brinell y una resistencia a la tracción de 28
kg/mm2, llegando hasta un alargamiento del 40%.
|
Al
microscopio se observa como granos poligonales claros.
La ferrita
también aparece como elemento eutectoide de
la perlita formando láminas paralelas separadas por otras láminas de cementita.
En los
aceros hipoeutectoides templados, puede aparecer mezclada con la martensita
cuando el temple no ha sido bien efectuado.
CEMENTITA
(Fe3C)
Es carburo
de hierro Fe3C y contiene 6.67% C.
Es el
microconstituyente más duro y frágil de los aceros, alcanzando
una dureza Brinell de 700 (68 Rc) y cristaliza en la red ortorrómbica.
.
|
PERLITA
Es el
microconstituyente eutectoide formado por capas alternadas de
ferrita y cementita.
Compuesta
por el 88 % de ferrita y 12 % de cementita, contiene el 0.8%C.
Tiene una
dureza de 250 Brinell, resistencia a la tracción de 80 kg/mm2 y
un alargamiento del 15%.
La perlita
aparece en general en el enfriamiento lento de la austenita y por la
transformación isotérmica de la austenita en el rango de 650 a 723°C.
Su nombre se
debe a las irisaciones que adquiere al iluminarla, parecidas a las perlas.
Si el enfriamiento es rápido
(100-200°C/seg.), la estructura es poco definida y se denomina SORBITA.
Si la perlita laminar se somete a un
recocido a temperatura próxima a 723°C, la cementita adopta la forma de
glóbulos incrustados en la masa de ferrita, denominándose perlita globular.
AUSTENITA
Es el constituyente más
denso de los aceros y está formado por una solución sólida por
inserción de carbono en hierro gamma.
La cantidad de carbono disuelto,
varía de 0.8% al 2% C que es la máxima solubilidad a la temperatura
de 1130°C. No es estable a la temperatura ambiente.
La austenita cristaliza en la red
FCC, con una dureza de 300 Brinell, una resistencia a la tracción de 100 kg/mm2 y
un alargamiento del 30 %, no es magnética.
.
|
MARTENSITA
Es el constituyente de los aceros
templados; está conformado por una solución sólida sobresaturada de carbono
o carburo de hierro en ferrita y se obtiene por enfriamiento rápido de los
aceros desde su estado austenítico a altas temperaturas.
El contenido de carbono suele variar
desde muy poco carbono hasta el 1% de carbono, sus propiedades físicas varían
con su contenido en carbono hasta un máximo de 0.7%C.
La martensita tiene una dureza
de 50 a 68 Rc, resistencia a la tracción de 170 a 250 kg/mm2 y
un alargamiento del 0.5% al 2.5%.
Es muy frágil y presenta un aspecto
acicular formando grupos en zigzag con ángulos de 60 grados.
TROOSTITA
Es un agregado muy fino de cementita
y ferrita que se produce por un enfriamiento de la austenita con una velocidad
de enfriamiento ligeramente inferior a la crítica de temple, por transformación
isotérmica de la austenita en el rango de temperatura
de 500ºC a 600ºC, o por revenido a 400ºC.
Sus propiedades físicas son
intermedias entre la martensita y la sorbita: tiene una dureza de 400
a 500 Brinell, una resistencia a la tracción de 140 a 175 kg/mm2 y
un alargamiento del 5 al 10%.
Es un constituyente nodular oscuro y
aparece generalmente acompañando a la martensita y a la austenita.
SORBITA
Es también un agregado fino de
cementita y ferrita.
Se obtiene por enfriamiento de la
austenita con una velocidad de enfriamiento bastante inferior a la crítica de
temple o por transformación isotérmica de la austenita en la zona
de 600ºC a 650ºC, o por revenido a la temperatura de 600ºC.
Su dureza es de 250 a 400
Brinell, su resistencia a la tracción es de 88 a 140 kg/mm2,
con un alargamiento del 10 al 20%.
Tanto la trostita como la sorbita
pueden considerarse como perlita de grano muy fino.
BAINITA
Es el constituyente que se obtiene
en la transformación isotérmica de la austenita cuando la temperatura del baño
de enfriamiento es de 250ºC a 500°C.
Se diferencian dos tipos de
estructuras:
- la bainita
superior de aspecto arborescente formada a 500ºC-580°C.
-la bainita
inferior, formada a 250ºC-400ºC tiene un aspecto acicular similar a la
martensita y constituida por agujas alargadas de ferrita que contienen delgadas
placas de carburos.
La bainita tiene una dureza variable
de 40 a 60 Rc comprendida entre las correspondientes a la perlita y a
la martensita.
Los constituyentes que pueden presentarse en los
aceros aleados son los mismos de los aceros al carbono, aunque la austenita
puede ser único contituyente y además pueden aparecer otros carburos simples y
dobles o complejos.
¿Qué son los constituyentes de los aceros? y ¿Relación de los constituyentes con los granos de los aceros?
La metalografía es la disciplina que estudia microscópicamente las características
estructurales de un metal o de una aleación. Sin duda, el microscopio es la herramienta más importante del metalurgista
tanto desde el punto de vista científico como desde el técnico. Es posible
determinar el tamaño de grano, forma y distribución de varias fases e inclusiones que tienen gran efecto
sobre las propiedades mecánicas del metal. La microestructura revelará el
tratamiento mecánico y térmico del metal y, bajo un conjunto de condiciones
dadas, podrá predecirse su comportamiento.
El tamaño de grano
tiene un notable efecto en las propiedades mecánicas del metal. Los efectos del
crecimiento de grano provocados por el tratamiento térmico son fácilmente
predecibles. La temperatura, los
elementos aleantes y el tiempo de impregnación térmica afectan el
tamaño del grano.
En metales, por lo general, es preferible un
tamaño de grano pequeño que uno grande. Los metales de grano pequeño tienen
mayor resistencia a la tracción, mayor dureza y se
distorsionan menos durante el temple, así como también son menos susceptibles
al agrietamiento. El grano fino es mejor para herramientas y dados. Sin embargo, en los aceros el
grano grueso incrementa la endurecibilidad, la cual es deseable a menudo para
la carburización y también para el acero que se someterá a largos procesos de trabajo en frío.
Todos
los metales experimentan crecimiento de grano a altas temperaturas. Sin
embargo, existen algunos aceros que pueden alcanzar temperaturas relativamente
altas (alrededor de 1800 F o 982 C) con muy poco crecimiento de grano, pero
conforme aumenta la temperatura, existe un rápido crecimiento de grano. Estos
aceros se conocen como aceros de grano fino. En un mismo acero puede producirse
una gama amplia de tamaños de grano.
La estructura cristalina es
la forma sólida de cómo se ordenan y empaquetan los átomos, moléculas, o iones.
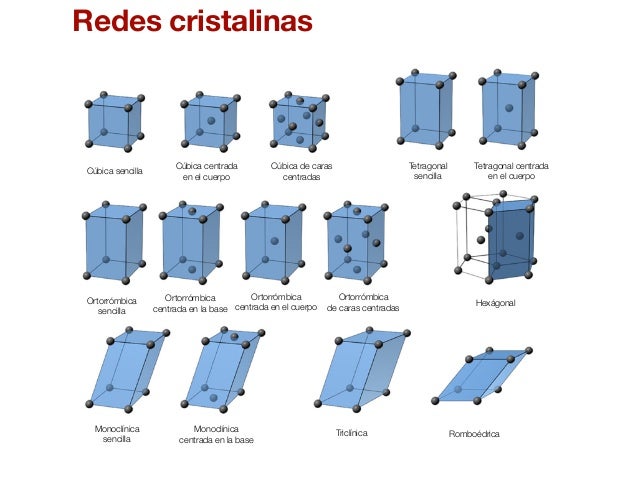
Tratamientos térmicos
en los aceros. Influencia en las propiedades mecánicas y por tanto en los
constituyentes
El
tratamiento térmico en el material es uno de los pasos fundamentales para que
pueda alcanzar las propiedades mecánicas para las cuales está creado. Este tipo
de procesos consisten en el calentamiento y enfriamiento de un metal en su
estado sólido para cambiar sus propiedades físicas. Con el tratamiento térmico
adecuado se pueden reducir los esfuerzos internos, el tamaño del grano,
incrementar la tenacidad o producir una superficie dura con un interior dúctil.
Los
tratamientos térmicos han adquirido gran importancia en la industria en
general, ya que con las constantes innovaciones se van requiriendo metales con
mayores resistencia tanto al desgastes como a la tensión. Los principales:
-Temple: Su
finalidad es aumentar la dureza y la resistencia del acero. Para ello, se
calienta el acero a una temperatura ligeramente elevada y se enfría luego
mas o menos rápidamente.
-Revenido: Solo se aplica a aceros
previamente templados, para disminuir ligeramente los efectos del temple,
conservando parte de la dureza y aumentar la tenacidad.
-Recocido: Consiste básicamente en
un calentamiento hasta la temperatura de austenizacion seguido de un
enfriamiento lento. Con este tratamiento se logra aumentar elasticidad,
mientras que disminuye la dureza.
-Normalizado: Tiene por objetivo
dejar un material en estado normal, es decir, ausencia de tensiones internas y
con una distribución uniforme del carbono.
Diagramas de enfriamiento (curvas de s)
Se
denomina curva TTT al diagrama que relaciona el tiempo y la temperatura
requeridos para una transformación isotérmica.
Los
diagramas TTT son gráficas que representan la temperatura frente al tiempo
(normalmente en escala logarítmica).
Son
muy útiles para entender las transformaciones de un Acero que se enfría isotérmicamente.
Así por ejemplo, en el caso del acero, y más concretamente para la fase
Austenita, que es inestable debajo de la temperatura de transformación
eutectoide, se necesita saber cuánto tiempo requerirá para empezar a
transformarse a una temperatura subcrítica específica, cuánto tiempo precisará
para estar completamente trasformada y cuál será la naturaleza del producto de
esta transformación.
Los diagramas tiempo-temperatura-transformación para
transformaciones isotérmicas y para transformaciones de enfriamiento continuo
se usan para predecir la microestructura y dureza deseadas.
